Rotary actuators are powered by electricity, fluid pressure, or even manually. They are used in a variety of applications, including valve operation, mobile hydraulic equipment, aircraft, and motion control systems.
In a fluid power system, rotary actuators act as output devices, delivering an oscillating motion within a limited range. They generate work through the application of fluid pressure against internal vanes.
The choice of rotary actuator depends on the specific application requirements, such as speed, torque, and load capacity.
What is a Rotary Actuator?
Rotary actuators are a type of mechanical device that uses hydraulics to convert energy into linear motion. They are commonly used in heavy equipment, such as bulldozers, which use them to lift and move heavy objects. Rotary actuators are also used in closed-loop control systems, where they provide high-speed and high-force operation.
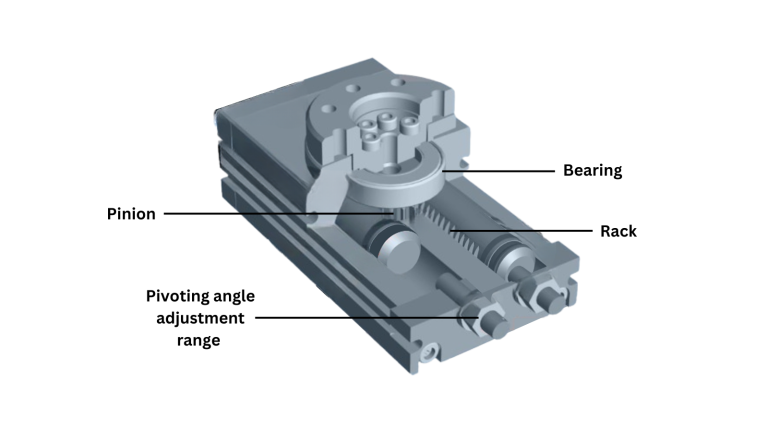
How Does a Rotary Actuator Work?
Fluid Power in Motion
Within a fluid power system, rotary actuators function as output devices, delivering an oscillating motion within a limited range (think one full revolution). Right-rotary actuators generate work through direct fluid pressure against internal vanes, utilizing energy over distance. Imagine them as providers of rotating or angular movement – strokes within defined angles – generating a special kind of rotational work called torque.
Circuitry Simplified
Take a simple rotary actuator circuit diagram, where applied force translates to torque. When these actuators operate at low speeds with high torque, output torque becomes the key parameter for identification and rating. For choosing the right one, speed often takes a backseat to specific application needs.
Torque Talk
Measuring torque typically involves foot-pounds. For example, a two-foot-radius rotary actuator lifting a 200-pound weight would require 400 lb•ft of torque to do the job. Understanding this system-to-output torque relationship empowers designers to select the perfect actuator for each unique application.
Types of Rotary Actuators
Manual Rotary Actuator
Often using worm drives for amplified torque in manual valve closure, these actuators are common on ball valves and quarter-turn butterflies. Their self-locking capabilities and large hand wheels make them worker-friendly. In the valve industry, they’re sometimes called manual overrides or gear operators.
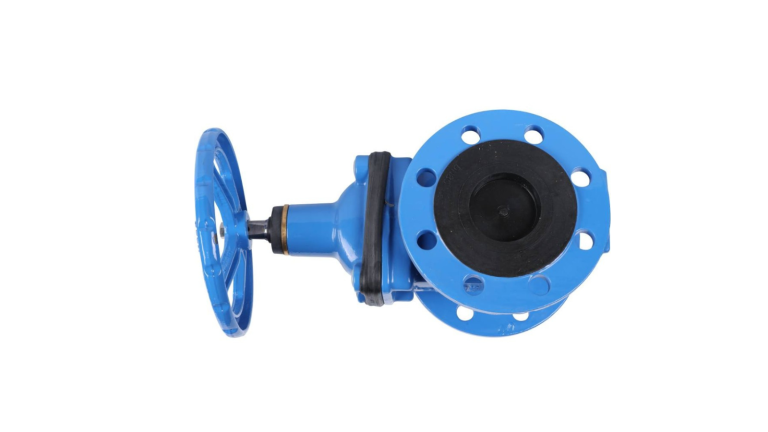
Electric Rotary Actuator
Driven by electromagnetic power, electric rotary actuators rotate components. They offer indexing and control capabilities, allowing for multiple position stops with strokes. Their rotating element can be a circular shaft or a table, with shafts often featuring keyways and tables offering bolt patterns for mounting additional components. Specifications include voltage supply, maximum torque, repeatability, load capacity, operating temperature, rotation angle, and linear stroke. These actuators find diverse applications, from high-power switching gears to the automotive industry and packaging.
Fluid-Powered Rotary Actuators
Also known as pneumatic or hydraulic rotary actuators, these utilize fluid power delivered to cylinders to shift scotch yokes and rack-and-pinion assemblies or to rotors for straight shaft actuation. They typically move between 90° and 360° stops, based on the specific component or valve’s rotation requirements.
Rack and Pinion Rotary Actuators
These mechanical devices primarily control dampers or valves in industrial settings. The rack & pinion, a couple of gears, converts linear motion to rotational. A linear gear bar (the rack) connects teeth on a round gear (the pinion). When linear force is applied to the rack, the pinion rotates.
Scotch Yoke Rotary Actuators
This actuator features a sliding bar connected to a valve at one end and a yoke at the other, which includes a slot for a block that slides back and forth. The block is connected to a piston, so when the piston moves, the block drives the yoke, turning it and moving the bar to open the valve. Applications include oil and gas (valve activation for flow separation), mining (valve activation for separating nozzles), and water and wastewater (valve activation for separating feed lines, tanks, and filters).
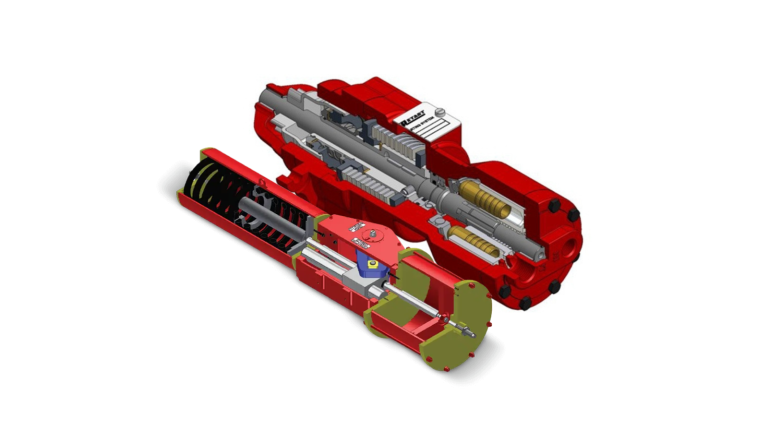
Helical Actuators
Using a set of helical gears and a cylinder, this actuator converts linear input to an oscillating, rotary output. The cylinder contains three rotating pins and three helical slots machined within the outermost tube, which also features three keys to prevent excessive movement. When the cylinder moves, air force pushes down on the outermost cylinder for valve opening and squeezes a spring. When the air force is released, the spring pushes the valve to close again.
Vane Rotary Actuator
These combine the muscle of pressurized hydraulic fluid with the control of an electric motor. The electrical energy powers the motor, which controls a hydraulic pump that supplies the pressurized fluid for operating the valve. This self-contained system eliminates the need for a separate hydraulic power unit, simplifying design and enhancing reliability and safety.
Vane Variety
Pneumatic and hydraulic vane actuators use one or two vanes connected to a hub in a circular chamber or wedge shape, allowing vane rotation from 90 to 280 degrees. In these actuators, the hub simply rotates between stops using oil or air force to generate motion at the output stem. A double-vane actuator includes two opposite vanes for more torque but limited rotation compared to a single-vane actuator within a full circular chamber. Vane actuators are space-efficient and often used for transferring, clamping, or placing light loads in medium-speed applications.
Pros and Cons of Rotary Actuators
Rotary actuators, despite their versatility, come with their own set of advantages and disadvantages. Here’s a breakdown to help you decide if they’re the right fit for your application:
1. Advantages
Durable and Powerful
Rotary actuators boast exceptional durability and deliver relatively high torque for their size, minimizing maintenance needs.
Angular Agility
Their rotational capabilities allow them to move objects smoothly through any desired angle, offering greater flexibility compared to linear actuators.
Stable Performance
Once activated, rotary actuators maintain excellent stability even at low speeds, ensuring consistent operation.
Smooth Motion
They provide smooth acceleration and deceleration, making them ideal for applications that require precise control of movement.
Easy Adjustments
Rotary actuators equipped with stepping motors allow for simple adjustments in speed and position, enhancing their adaptability.
2. Disadvantages
Torque Limitations
Vane actuators, a common type, have limited torque and rotation compared to rack and pinion actuators, making them suitable only for light loads and medium-speed applications.
Load Capacity
Due to the use of small bushing-type bearings, these actuators can only handle light loads.
Minimal Shock Resistance
They exhibit minimal shock capacity, making them less suitable for applications with high impact forces.
External Stops
For high-speed applications, external stops are often necessary to ensure safe and controlled operation.
Rotary actuators offer durability, powerful torque, and flexibility in movement, making them valuable assets in various applications. However, their limitations in terms of torque, load capacity, and shock resistance should be carefully considered before making a selection.
Endnote
Rotary actuators, with their diverse functionalities and impressive capabilities, are undoubtedly valuable tools across various industries. However, navigating the different types and understanding their unique strengths and limitations is crucial for making an informed decision.
By carefully considering your specific application’s requirements, including speed, torque, load capacity, and operating environment, you can select the perfect rotary actuator that delivers optimal performance and efficiency. Remember, factors like the presence of shock forces or the need for high-speed operations might necessitate additional considerations like external stops.
If you’re unsure about which type of rotary actuator best suits your needs, don’t hesitate to consult with industry experts or manufacturers.